WHY SHOULD YOU ATTEND?
A good CAPA process can make the quality management system, and an inadequate one can break it. Deficient CAPA is a leading cause of ISO 9001 and IATF 16949 audit findings, as well as FDA Form 483 observations, and warning letter citations for medical device companies. The latter are escalations of observations, and deficient or absent CAPA is cited frequently in them. This comes as no surprise because, if the CAPA process is not adequate, comprehensive corrective action including identification and removal of root causes will not be taken for quality issues, audit findings (and failure to resolve an audit finding is itself a quality system nonconformance), customer complaints, and other issues. Actions to address risks and opportunities will also fall short. A good CAPA process will, on the other hand, help to not only resolve problems but also to drive continual improvement and contribute to the bottom line.AREA COVERED
1. CAPA is a major source of ISO 9001 and IATF 16949 findings, and FDA Form 483 observations.2. Supplier and customer processes of the CAPA process such as management review, internal audit, and external customers.
3. Application of CAPA to all seven wastes of the Toyota production system allows the removal of these wastes with consequent bottom-line financial and performance-related results.
4. CAPA requires organizational support as depicted in Appendix A of CQI-20. An overview of this will be provided.
5. CQI-20 is arguably more effective than Six Sigma’s DMAIC process and will work on a much wider range of problems and opportunities.
6. CQI-20 is a nine-step process, the elements of which will be provided.
- The process begins with awareness of the problem. We can expand widely its range of applications by treating any gap between current performance and desired performance as a "nonperformance" thus allowing its application to any of the seven wastes of the Toyota production system. (Visser, Chris. 8D Problem Solving Explained, refers to a performance gap in this context.)
- Containment (step 4) is required only for poor quality.
- Look for three root causes. The escape root cause is why the problem reached an internal or external customer (assuming that it was not caught by the process that generated it). The occurrence root cause is why the defect was generated, or why there is some other gap between current and desired performance. The systemic root cause is why the planning process did not identify the issue previously.
- Select, test, and implement a corrective or preventive action. Apply the action to the related processes that might benefit from it (read across/ replicate, or best practice deployment).
7. The hatto (awareness or recognition), or Error Cause Removal (ECR) process is a much simpler process for problems or opportunities that can be resolved on the shop floor by the process owner.
8. Examples will be provided.
LEARNING OBJECTIVES
1. Know the central role of CAPA in the quality management system and its interactions with other processes of the quality management system.2. Know that inadequate CAPA is a principal source of ISO 9001 and IATF 16949 audit findings, and FDA
3. Form 483 observations and warning letters.
4. Know how CAPA applies to all seven Toyota production system wastes and not just poor quality.
5. Know and apply the elements of AIAG’s Effective Problem-Solving process. (Purchase of the manual from AIAG is highly recommended.)
6. Recognize the need to look for three rather than one root cause of any problem: the occurrence root cause (why it happened), the escape root cause (how the problem escaped to an internal or external customer), and the systemic root cause (why the planning process didn't anticipate the problem in advance). This goes well beyond the traditional approach of looking only for an occurrence's root cause.
• This is synergistic with process failure mode effects analysis (PFMEA) because the escape root cause relates to a deficiency in the process’ detection controls and the occurrence root cause to a deficiency in the process’ prevention controls. Removal of the root causes should usually update the PFMEA to reflect new or improved controls.
7. Deploy a separate process for problems that can be easily resolved on the shop floor by the process owner. The Japanese hatto (“recognition or awareness” of a problem or opportunity) and identical Error Cause Removal processes are available off the shelf.
8. The handout will include an appendix with an overview of the related 8D (Eight Disciplines) process; this is very similar to CQI-20.
WHO WILL BENEFIT?
- Managers.
- Executives.
- Engineers, and others with responsibility for the quality management system.
- Also, all manufacturing, users of ISO 9001 and IATF 16949, and FDA-regulated industries. Services also might benefit.
2. Supplier and customer processes of the CAPA process such as management review, internal audit, and external customers.
3. Application of CAPA to all seven wastes of the Toyota production system allows the removal of these wastes with consequent bottom-line financial and performance-related results.
4. CAPA requires organizational support as depicted in Appendix A of CQI-20. An overview of this will be provided.
5. CQI-20 is arguably more effective than Six Sigma’s DMAIC process and will work on a much wider range of problems and opportunities.
6. CQI-20 is a nine-step process, the elements of which will be provided.
- The process begins with awareness of the problem. We can expand widely its range of applications by treating any gap between current performance and desired performance as a "nonperformance" thus allowing its application to any of the seven wastes of the Toyota production system. (Visser, Chris. 8D Problem Solving Explained, refers to a performance gap in this context.)
- Containment (step 4) is required only for poor quality.
- Look for three root causes. The escape root cause is why the problem reached an internal or external customer (assuming that it was not caught by the process that generated it). The occurrence root cause is why the defect was generated, or why there is some other gap between current and desired performance. The systemic root cause is why the planning process did not identify the issue previously.
- Select, test, and implement a corrective or preventive action. Apply the action to the related processes that might benefit from it (read across/ replicate, or best practice deployment).
7. The hatto (awareness or recognition), or Error Cause Removal (ECR) process is a much simpler process for problems or opportunities that can be resolved on the shop floor by the process owner.
8. Examples will be provided.
2. Know that inadequate CAPA is a principal source of ISO 9001 and IATF 16949 audit findings, and FDA
3. Form 483 observations and warning letters.
4. Know how CAPA applies to all seven Toyota production system wastes and not just poor quality.
5. Know and apply the elements of AIAG’s Effective Problem-Solving process. (Purchase of the manual from AIAG is highly recommended.)
6. Recognize the need to look for three rather than one root cause of any problem: the occurrence root cause (why it happened), the escape root cause (how the problem escaped to an internal or external customer), and the systemic root cause (why the planning process didn't anticipate the problem in advance). This goes well beyond the traditional approach of looking only for an occurrence's root cause.
• This is synergistic with process failure mode effects analysis (PFMEA) because the escape root cause relates to a deficiency in the process’ detection controls and the occurrence root cause to a deficiency in the process’ prevention controls. Removal of the root causes should usually update the PFMEA to reflect new or improved controls.
7. Deploy a separate process for problems that can be easily resolved on the shop floor by the process owner. The Japanese hatto (“recognition or awareness” of a problem or opportunity) and identical Error Cause Removal processes are available off the shelf.
8. The handout will include an appendix with an overview of the related 8D (Eight Disciplines) process; this is very similar to CQI-20.
- Managers.
- Executives.
- Engineers, and others with responsibility for the quality management system.
- Also, all manufacturing, users of ISO 9001 and IATF 16949, and FDA-regulated industries. Services also might benefit.
Speaker Profile
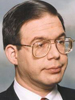
William A. Levinson, P.E., is the principal of Levinson Productivity Systems, P.C. He is an ASQ Fellow, Certified Quality Engineer, Quality Auditor, Quality Manager, Reliability Engineer, and Six Sigma Black Belt. He is also the author of several books on quality, productivity, and management, of which the most recent is The Expanded and Annotated My Life and Work: Henry Ford’s Universal Code for World-Class Success.
Upcoming Webinars
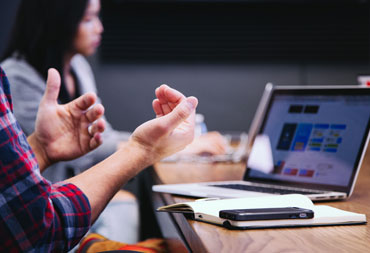
Performance of Root Cause Analysis, CAPA, and Effectiveness…
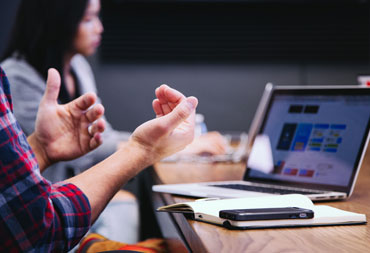
Stress, Change And Team Resilience Through Humor: An Intera…
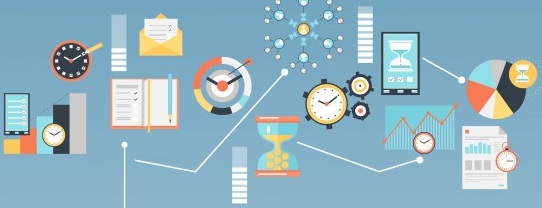
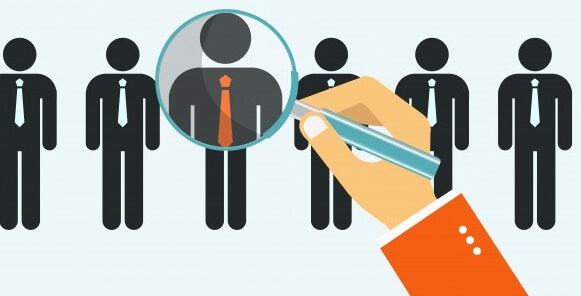
Future-Forward Onboarding: Navigating Success in 2024 for M…

Utilizing HR Metrics to Illustrate & Improve Human Resource…
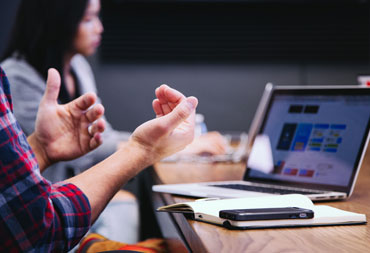
Basics of Investigational Drug Services
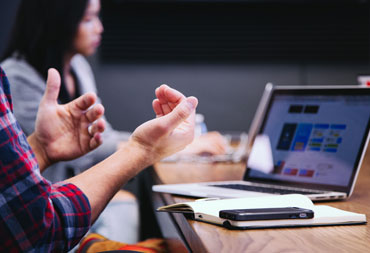
Data Integrity and Privacy: Compliance with 21 CFR Part 11,…
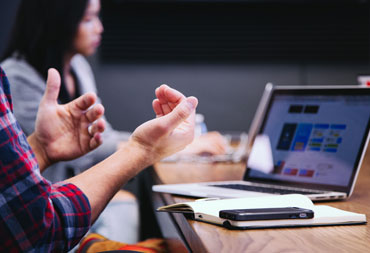
Excel - Pivot Tables - The Key To Modern Data Analysis and …
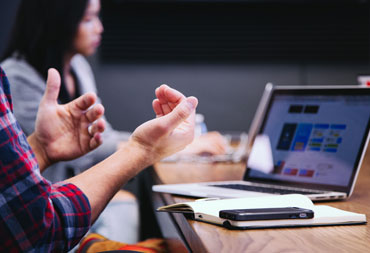
Employee Business Expense Reimbursement (2024 Updates)
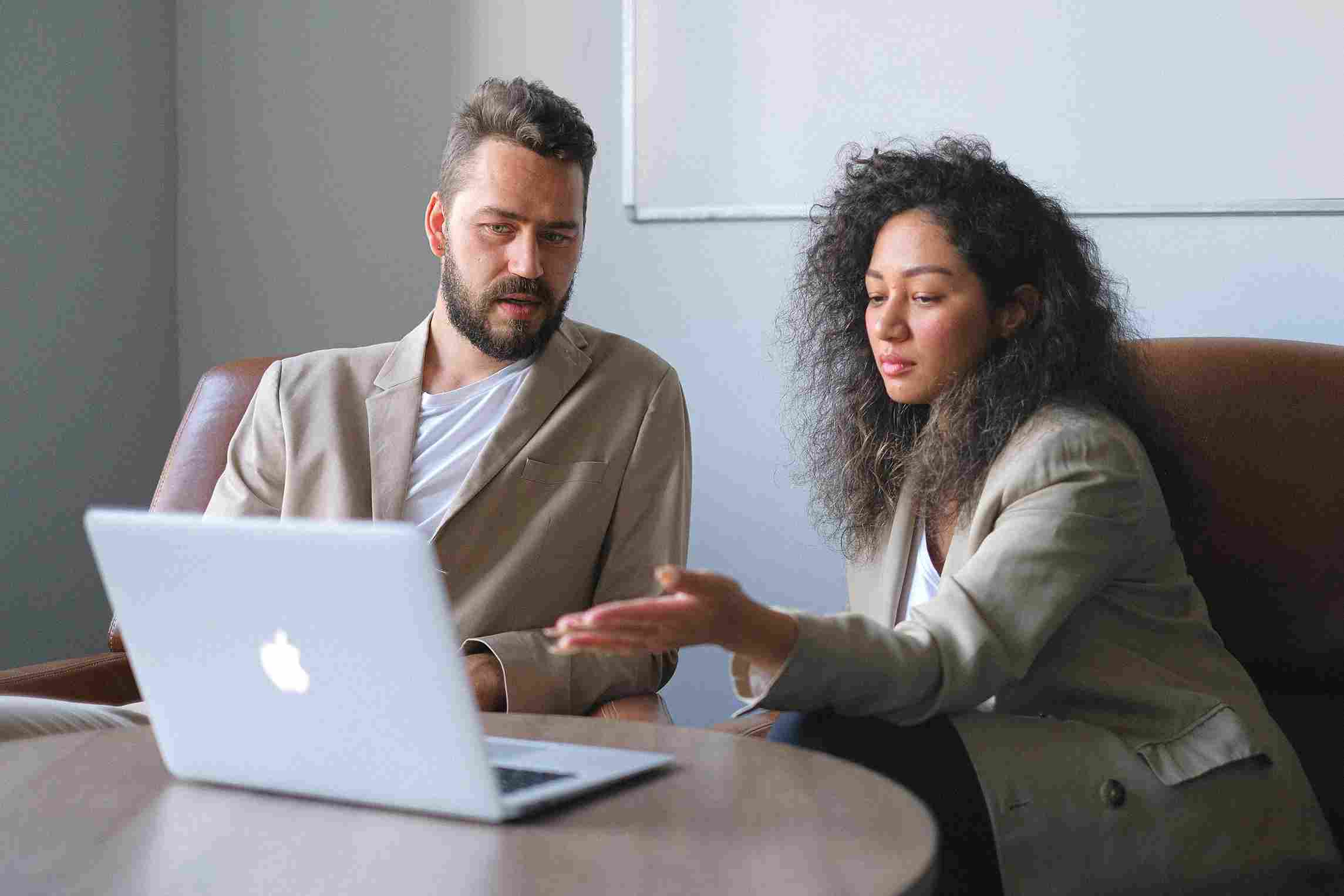
Stay Interviews: A Powerful Engagement and Retention Tool
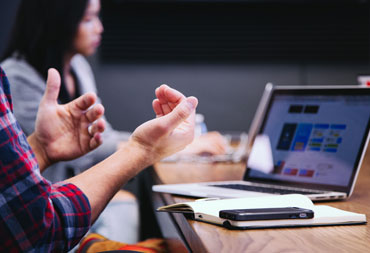
The Magic of Engagement: The Profitability of An Engaged Wo…
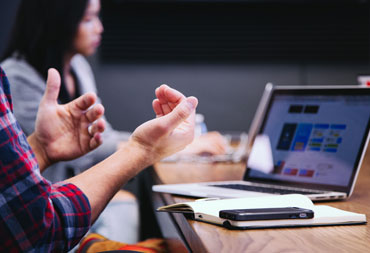
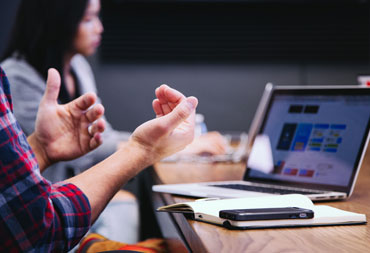
Risk Management in the FedNow® Instant Payments Era
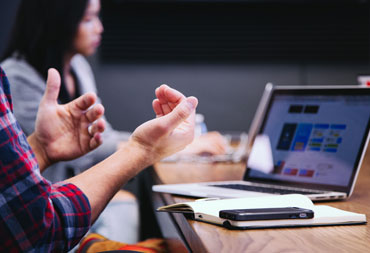
Marketing to Medicare or Medicaid Beneficiaries - What You …

FFIEC BSA/AML Examination Manual: What Compliance Officers …
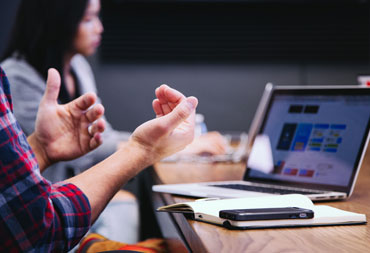
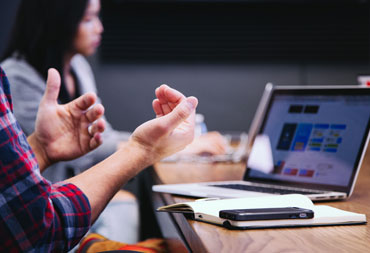
Gossip-Free: Leadership Techniques to Quell Office Chatter
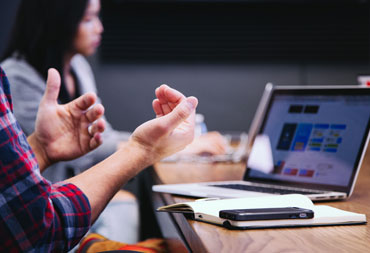
2-Hour Virtual Seminar on The Complexity and Interplay Amon…
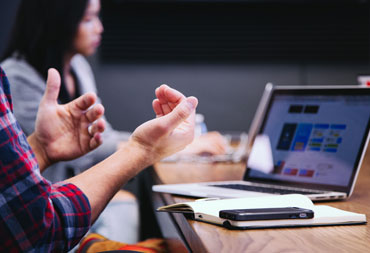
How to Prepare For and Host a FDA Inspection and Respond to…
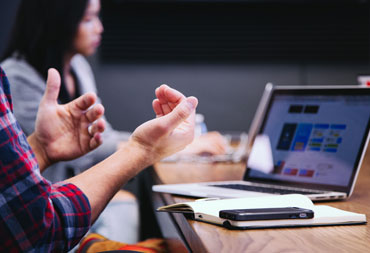
Pay Transparency: The Why and How for HR Pros
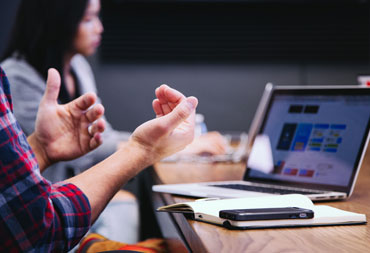
FDA Compliance And Laboratory Computer System Validation
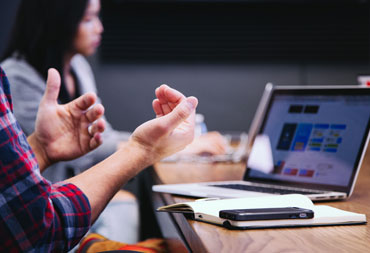
Stark After Tuomey, Intermountain Health, Akron General, Pr…
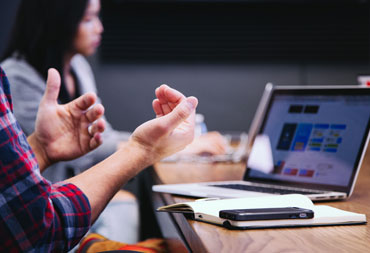
Project Management for Non-Project Managers - Scheduling yo…
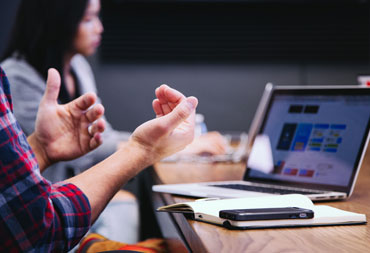
Your Workplace Culture for 2024: If You Don't Get It Right,…
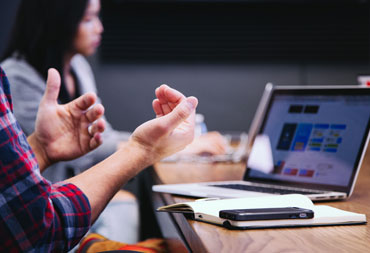
Tech Etiquette for Customer Service Help Desk Professionals
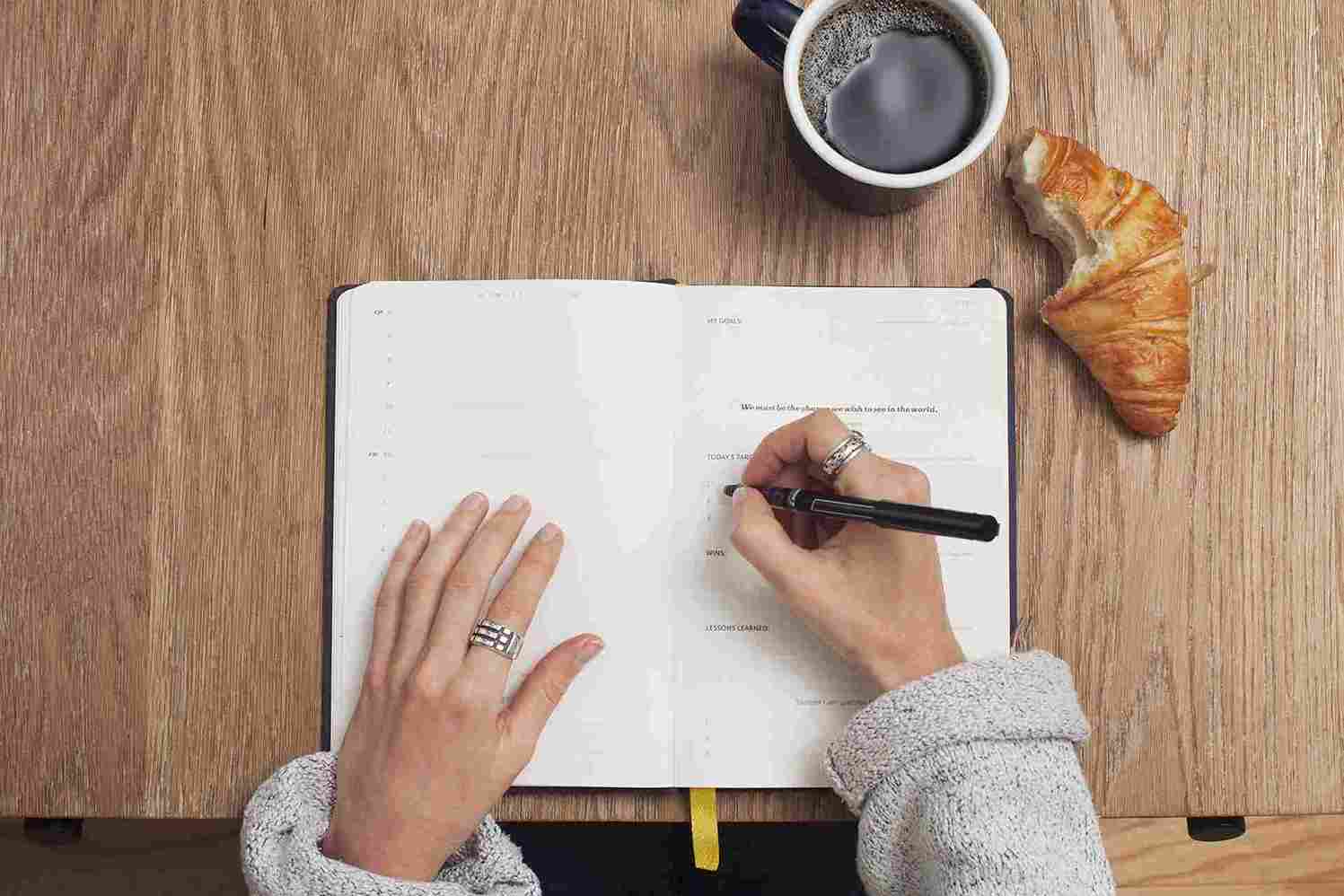
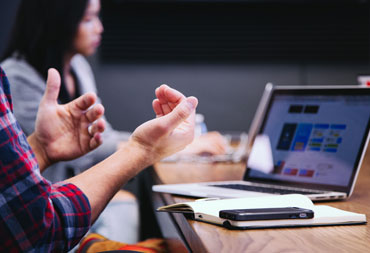
Implementing an Effective Succession Plan to Identify, Deve…
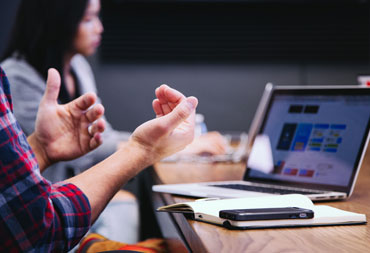
Impact of machine learning in pre-clinical research and reg…
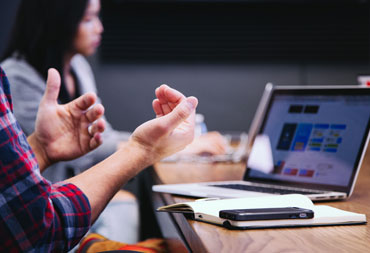
4-Hour Virtual Seminar on Transformational Leadership - The…
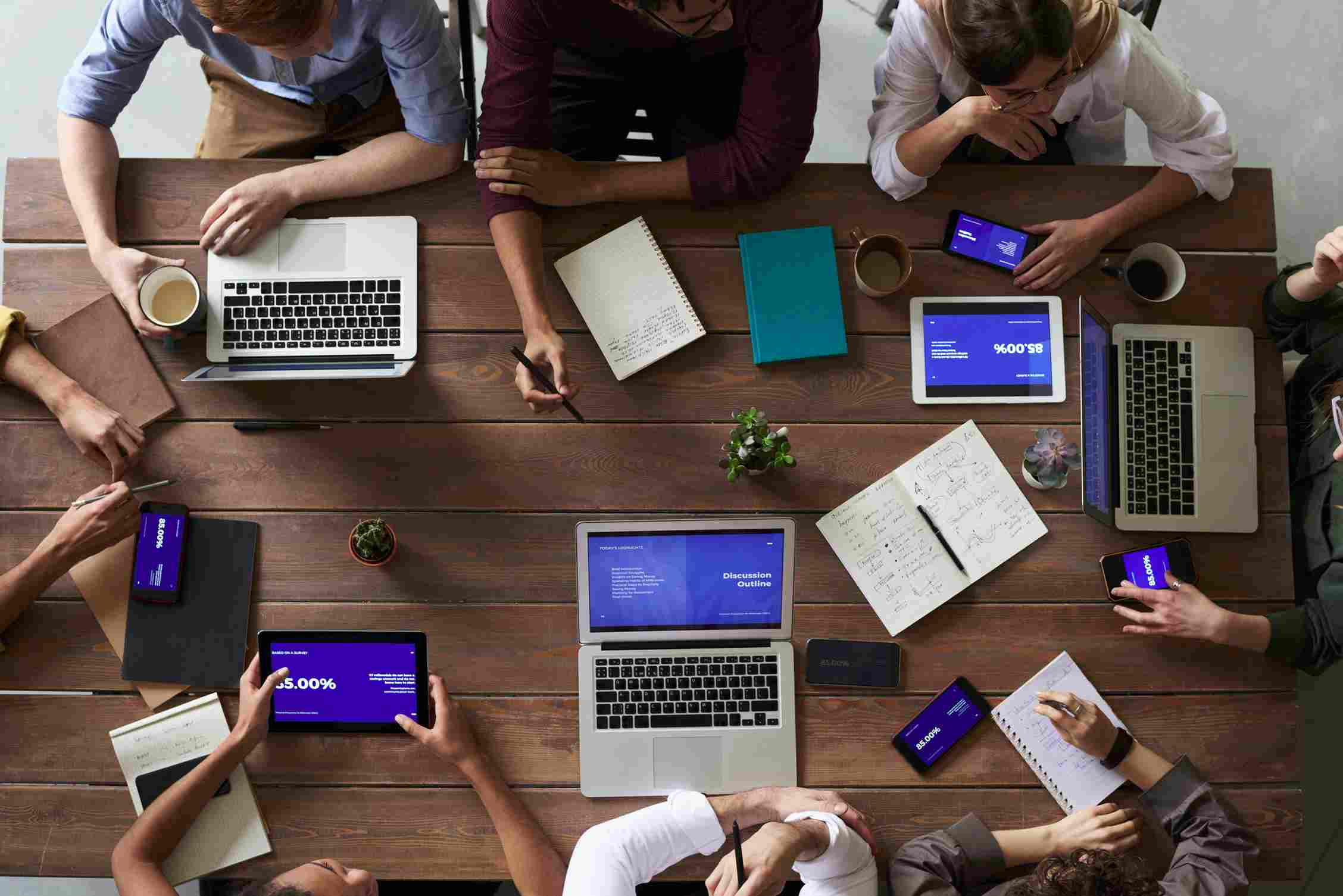
Project Management for administrative professionals
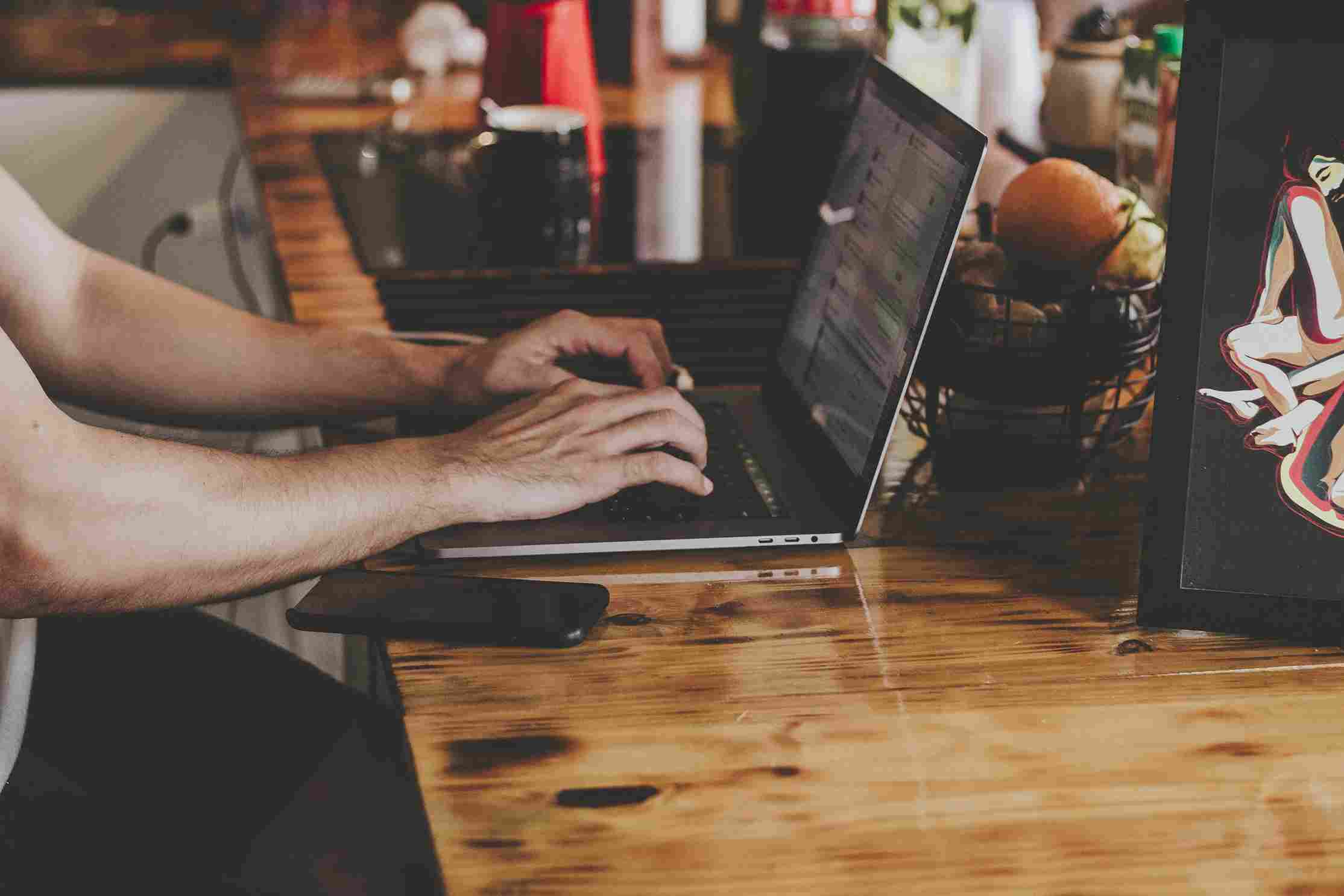
3-Hour Excel Automation Boot Camp: Top Ten Excel Functions …
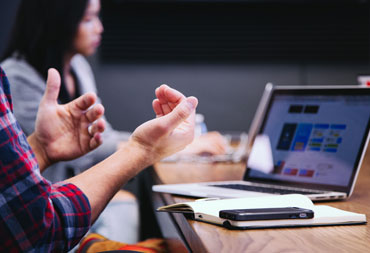
Work Well Remotely: Healthy Habits at Home
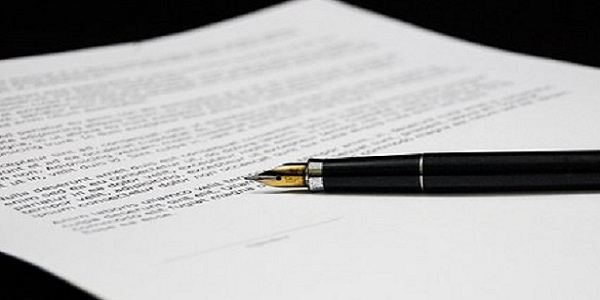
IRS Form 1099 Reporting: Compliance Requirements
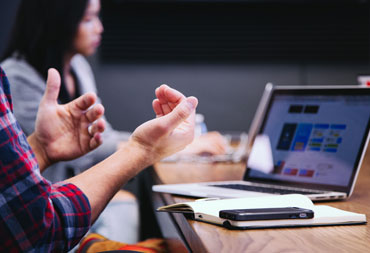
Understanding Emerging Payments Fraud and Risk Management
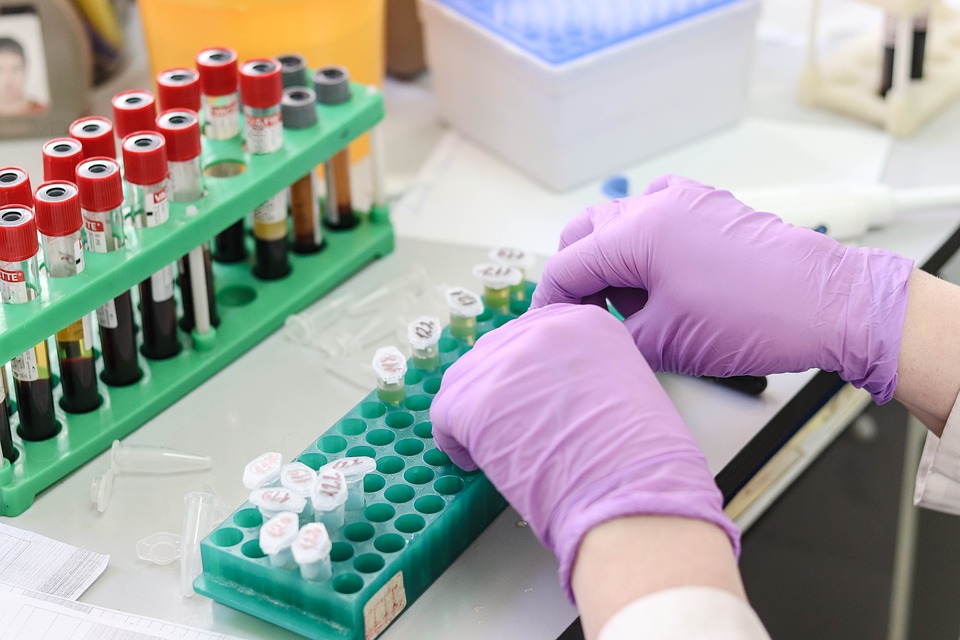
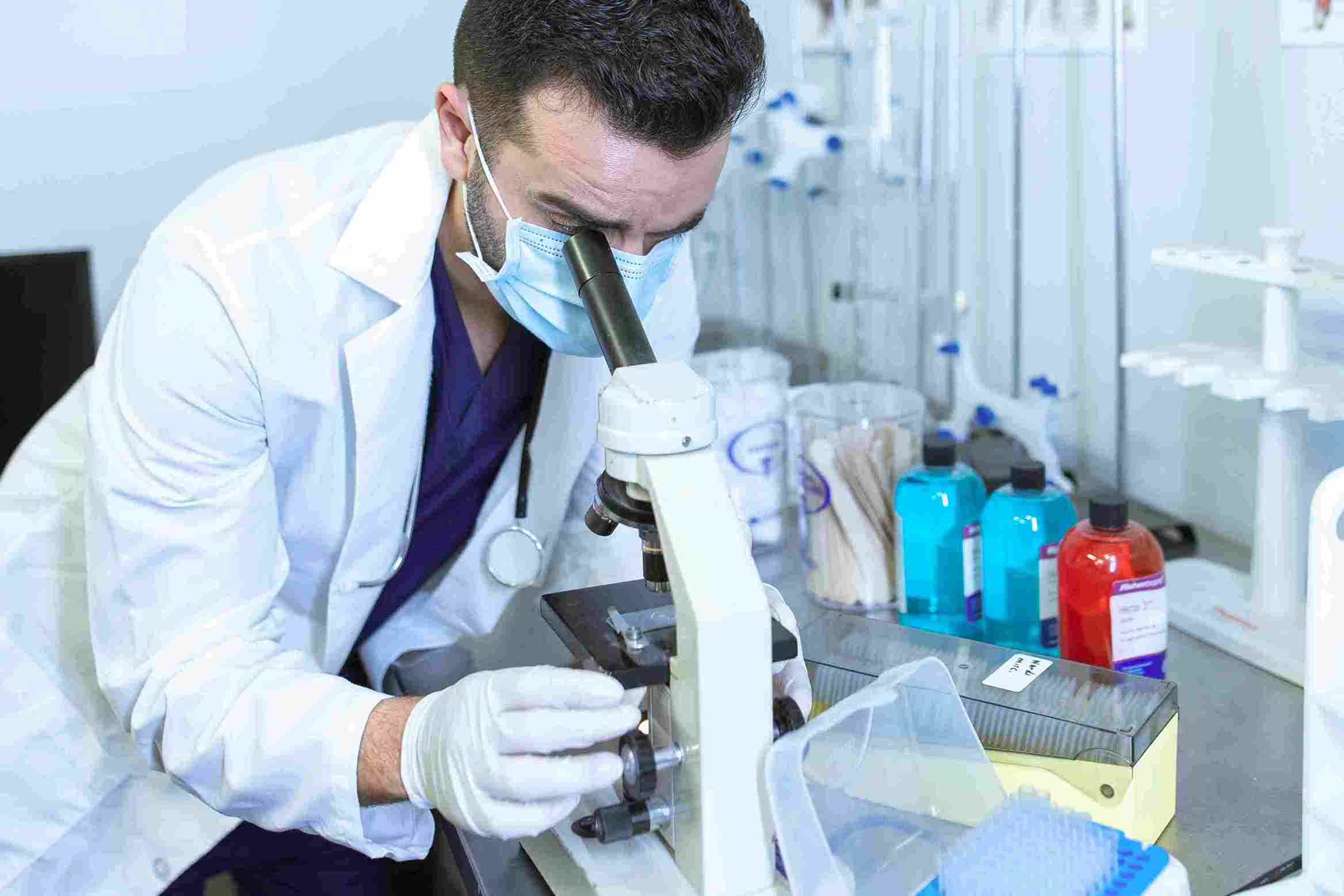
Sunshine Act Reporting - Clarification for Clinical Research
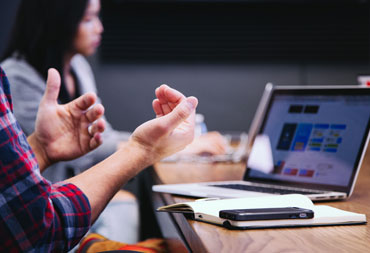
Navigating FDA Inspections: From SOP to 483
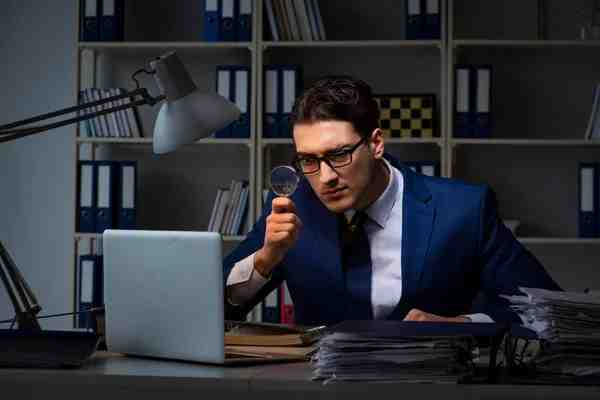
Implementing an Effective Human Error Reduction Program
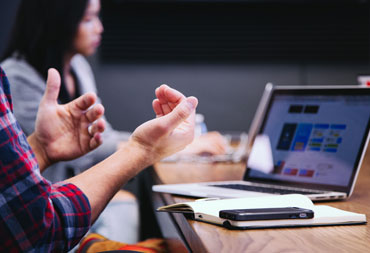
Fair Debt Collection Practices Act (FDCPA)
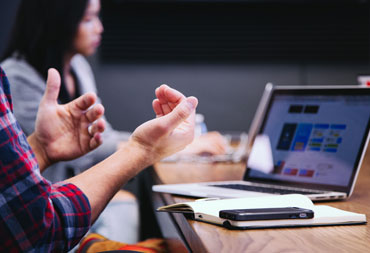
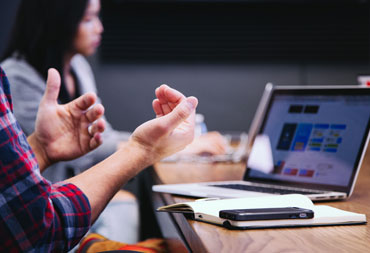
Complying with the NEW I-9 and E-Verify Regulations - The I…
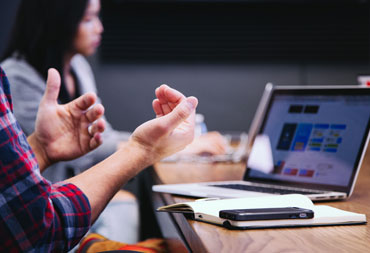
SOPs - How to Write Them to Satisfy those Inspectors
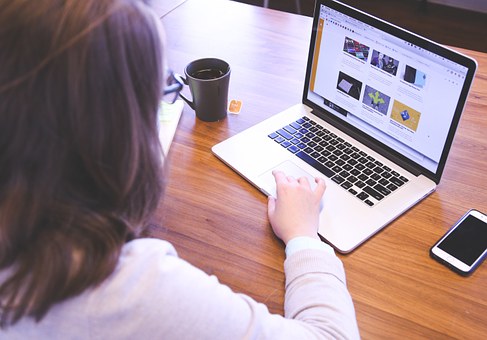
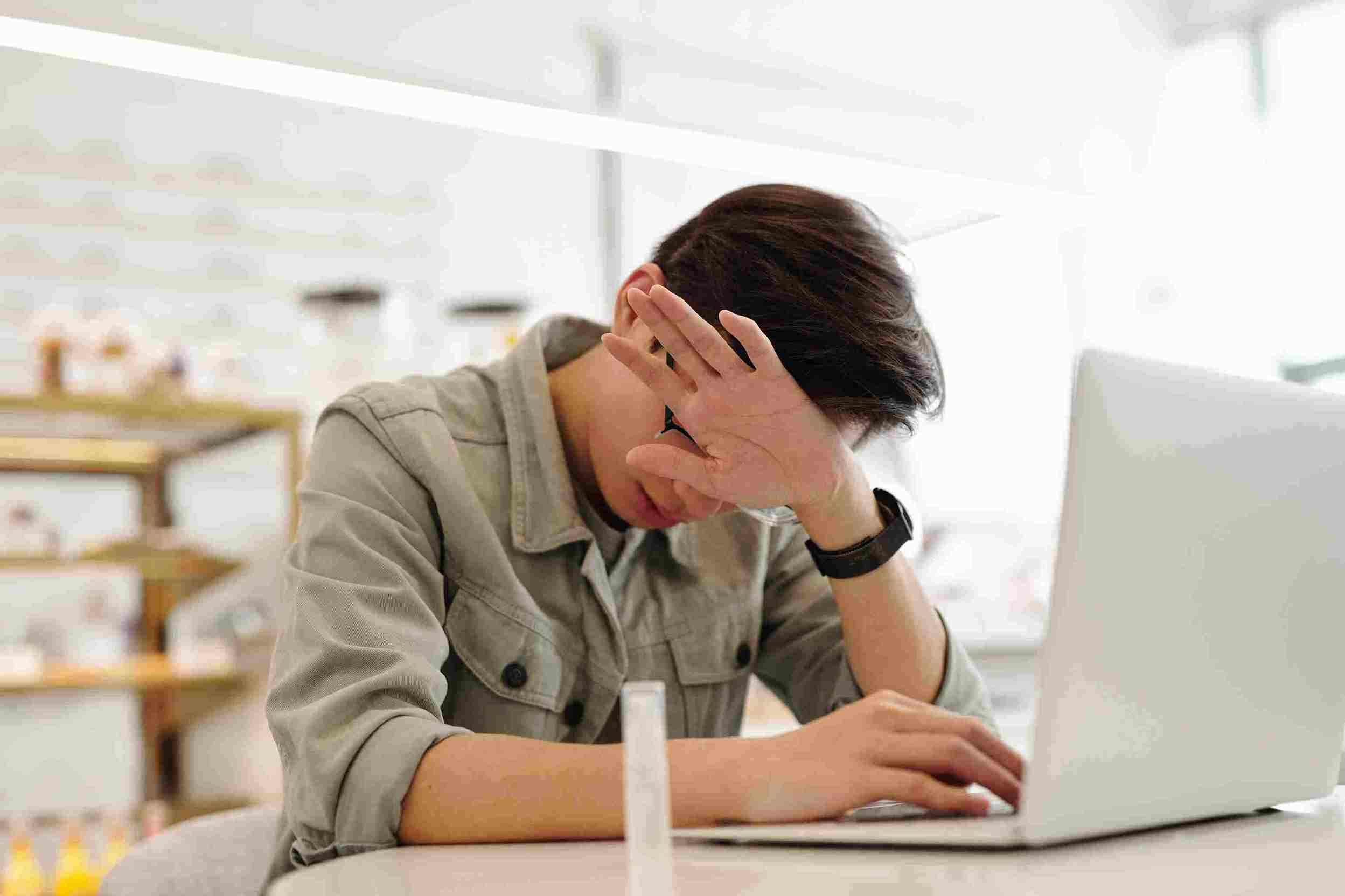
Stressed Out: How to Handle Conflict, Difficult People and …

California Meal and Rest Breaks: What You Dont Know Can Cos…
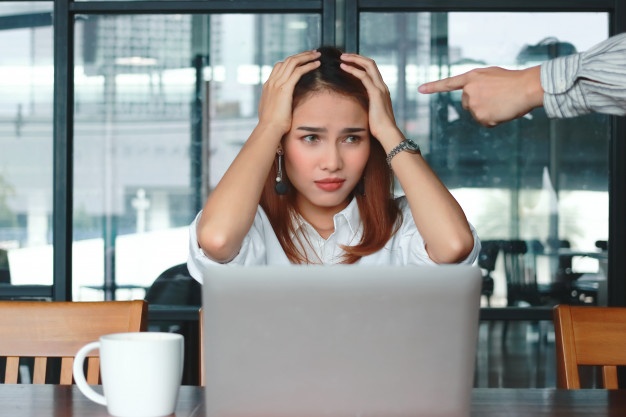
Harassment, Bullying, Gossip, Confrontational and Disruptiv…
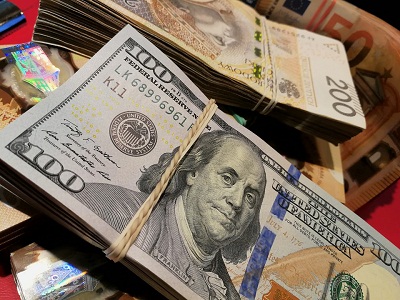
Why EBITDA Doesn't Spell Cash Flow and What Does
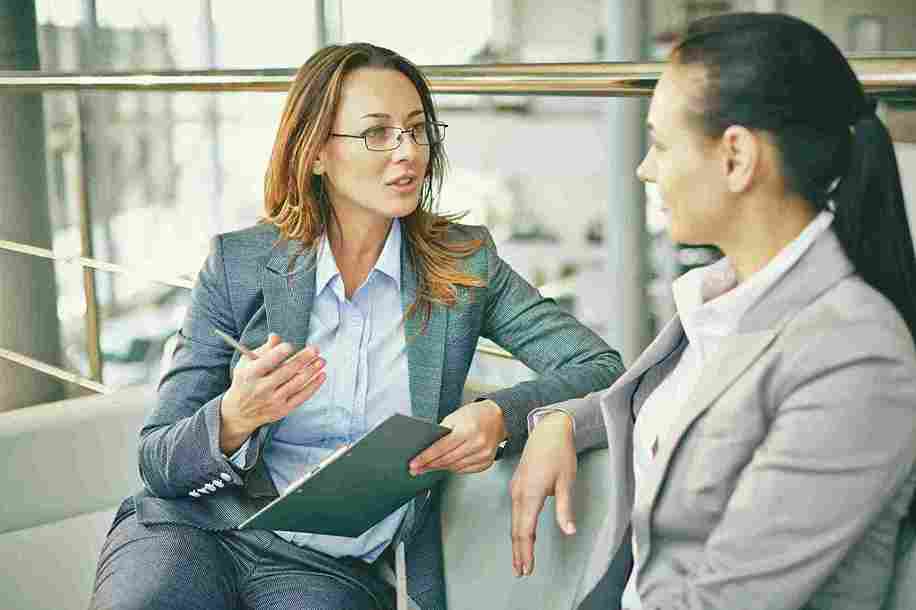
Using Behavior Based Interviewing for Finding the Best Matc…
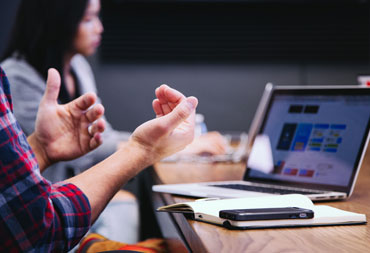
Onboarding is Not Orientation: How to Improve Your New Hire…
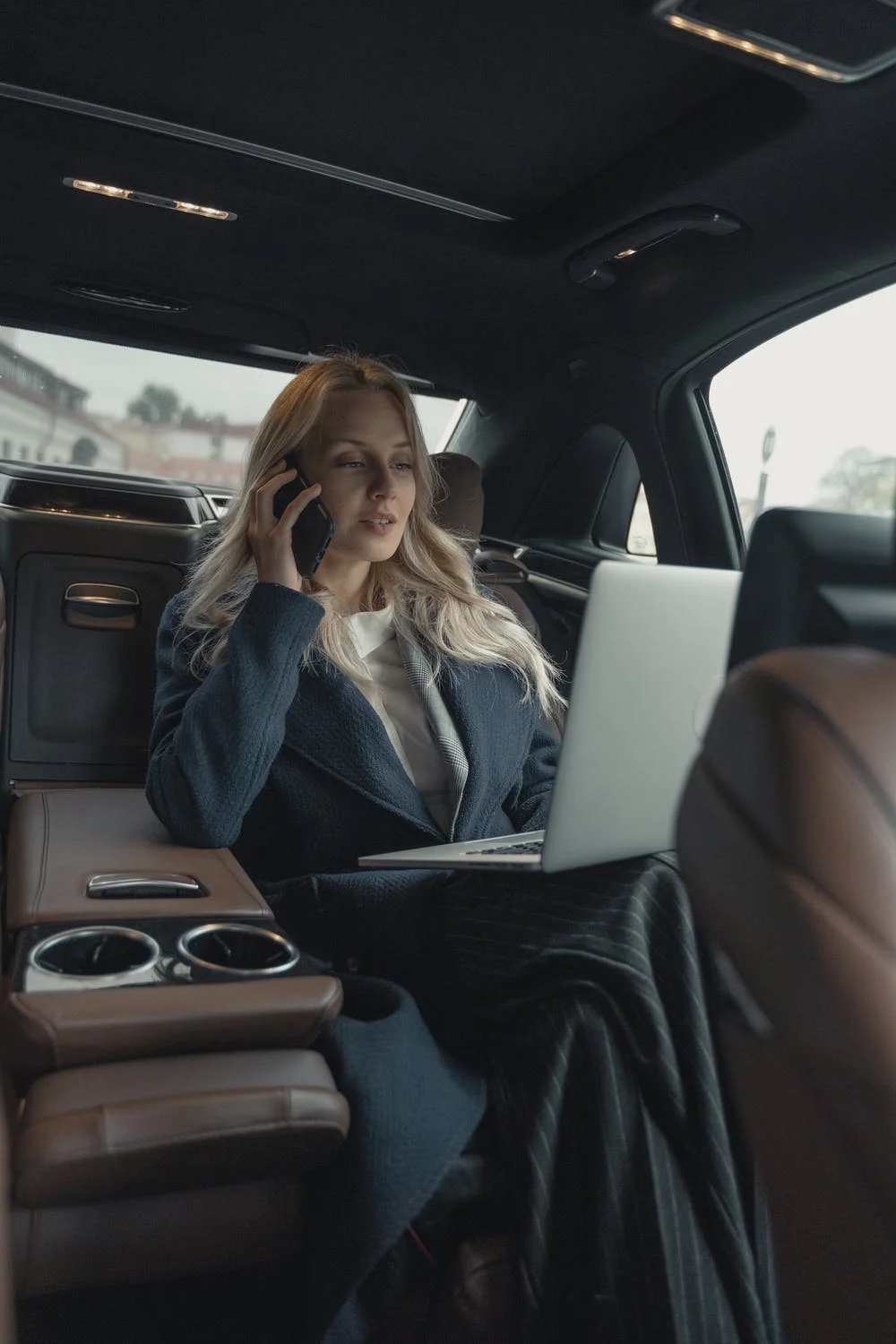
Dealing With Difficult People In Life & Work